Digital Twin in the space sector is now an almost compulsory technology. Testing virtually is an absolute cost saving especially in that field in which one small step for a man can mean one giant budget for a space organisation.
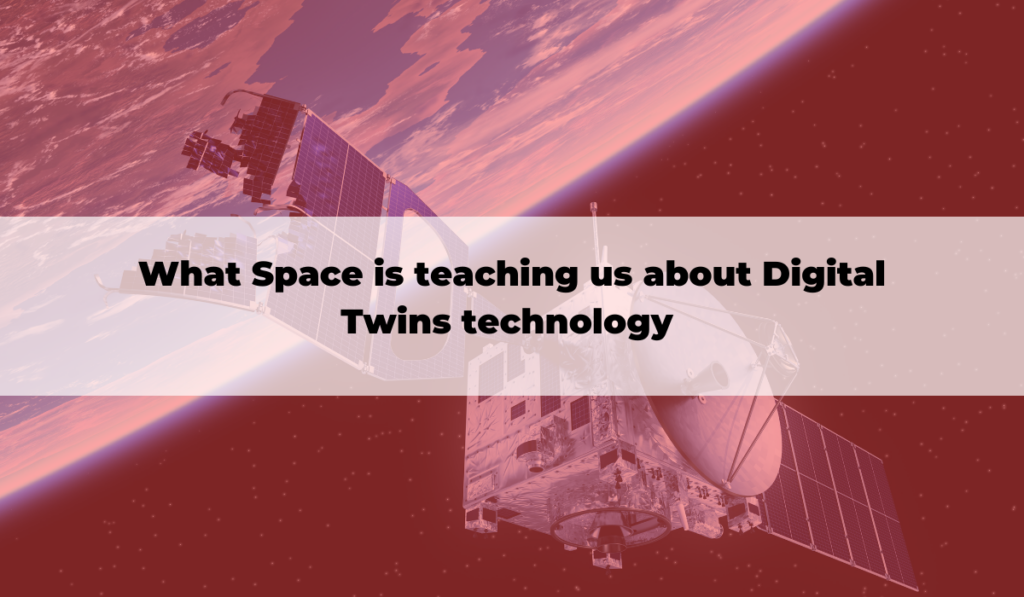
Picture that moment on July 20, 1969, when Neal Amstrong squeezed the dusty soil of the moon with his boots and left the most known footprint of the Universe. By the way, boots jettisoned before liftoff because of weight concerns were made of many materials and 21 interior layers because no one knew exactly what the moon was made of. This fantastic achievement of bringing people on the Earth satellite was possible thanks to a huge effort of engineering and manufacturing to conceive the Apollo Lunar Module. At the time, Grumman Aircraft Engineering, a Long Island, New York-based military aircraft contractor, was selected to bring men to the moon. In fact, the company was creating attack aircraft for the US Navy during World War II, the Korean War, and the Vietnam War. The module was first designed in 1962, went into production in 1963, and first tested in 1968. The first lunar descent occurred in May 1969, only a few months before the Apollo 11 mission. Despite the mission’s success, the Apollo Space program faced many accidents and terrible moments leading up to the loss of astronauts and eventually to the end of the program after many attempts to conquer space.
Digital twin technologies help us go back to the moon and beyond with more safety guarantees
The module that brought Amstrong and his two companions far away up in the sky measured 6.17 cubic meters of space. Over time, many experiences have been made to test our human limits and cope with small spaces. As a matter of fact, could you lock yourself in a fake small and narrow spaceship for about two years without possibly going out and sharing it with some fellows? That does not sound like an enjoyable trip. These experiences, however, have helped psychologists and future astronauts unveil the effect of confinements before a virus obliges us to practice it. MARS-500 is one of these experiments that took place between 2007 and 2011 together with Russia, ESA, and China to simulate a 520-day crewed mission with 6 persons on board. Sleep issues were one of the major problems. Would digital twins help to avoid this kind of experience? If you consider that some professional athletes are already twinned, we already have a lot of data about human behaviour. An ESA Discovery programme study aim to develop an immersive augmented/virtual reality viewer that uses 3D pose estimation to animate realistic avatars of people. This technology would support communications and monitoring – for example in areas like designing missions, assembly, integration, testing & verification of spacecraft, and in mission control. Safety is one of the top topics out there, every must be under control. Virtual twin scenarios and full digitalisation of every equipment would ensure the opportunity to recreate infinite situations the astronauts could face during their journey into the unknow.
This technology would support communications and monitoring – for example, in areas like designing missions, assembly, integration, testing & verification of spacecraft, and mission control. Safety is one of the top topics, and everything must be controlled. Virtual twin scenarios and full digitalisation of every piece of equipment would ensure the opportunity to recreate infinite situations the astronauts could face during their journey into the unknown.
A technology to better understand manufacturing processes
Be prepared to get knocked down with the piece of knowledge that you are about to read. At the beginning of this story, the Apollo Lunar Module was mentioned, as well as the fact that materials were left on the moon for weight concerns. This big metal can weigh 16 tons, the equivalent of three elephants. It was made of different materials, mainly aluminium, to protect the spaceship structure from temperature and micrometeoroids. Today, one of the most important materials for spacecraft is, and you won’t believe it, plastic. Naturally, weight savings is the first reason to use it. The type of plastic used is called Thermoplastic, which has the particularity of becoming pliable or mouldable at a certain elevated temperature. Thermoplastics are used for various spacecraft applications, such as bearings, optical lens centring rings, valve and regulator components, electrical insulators, radomes, and magnetometer components. The absolutely fascinating technique used to heat the plastic sheet is called the thermoforming process, and its two common forming methods are vacuum and pressure forming. Companies like Indaero Grupo Emergy European funds to better understand thermoforming processes by developing Machine Learning for Optimising Industrial Processes using Digital Twin technology.
Undoubtedly, digital twins can have a huge impact in the Space sector, optimizing processes and energy, simulating scenarios, and virtually engaging with all types of possible issues for astronauts to reduce the constant monitoring of the data produced by their journey and feel safer.
Marjorie Grassler