The promise of a tailored-made world dedicated to conceiving on demand products in a resilient and reliant way may pop-up in the manufacturing sector thanks to highly automated factories called micro factories.
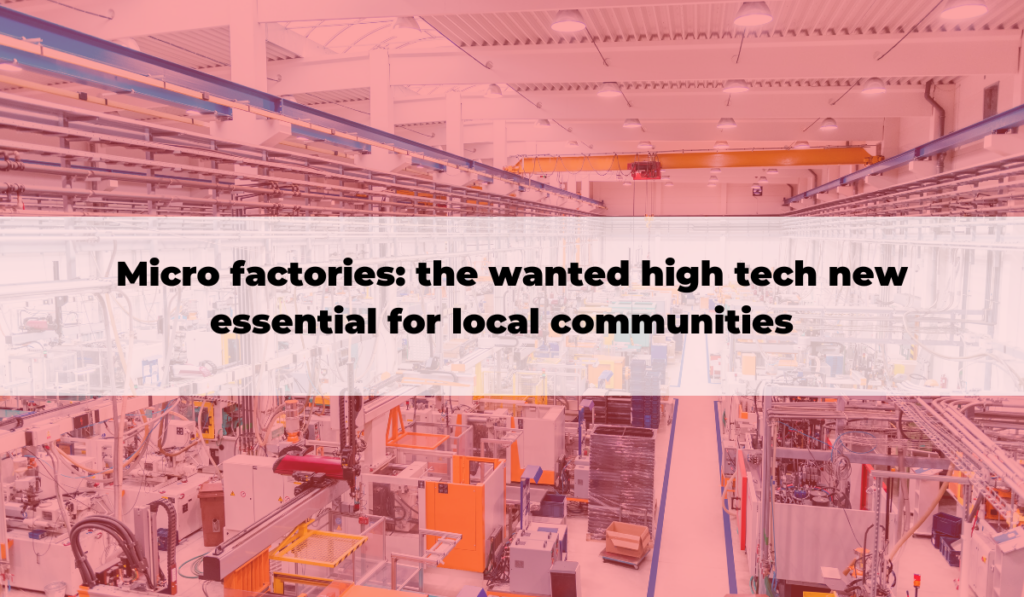
Industry 4.0 never fails to give you the impression that more will happen. History will say, as always, that there is nothing new on the horizon; that it is just a question of time or money or whatever other circumstances that have put the topic at the centre of the attention. Although with a bit of research, everything seems to have been thought already, scientists are truly the most creative people – technology evolution and massive investment have made again science fiction realistic. Now what? A new kind of factories is giving wings to the most ambitious projects with less money, less energy, less waste but most important acting local.
According to the World Economic Forum, Microfactories are small-to-medium, modular manufacturing facilities that use state-of-the-art technology like AI to optimise operations. World Manufacturing Foundation in its 2021 report on modular microfactories explains that the concept started to emerge in Japan in the nineties and is defined as a highly automated small-footprint facility which could be located in a small room to produce parts or consumer products. Nowadays, it seems to include also larger footprints with highly modular, flexible and automated facilities to produce small-batches.
4 reasons micro factories can make a difference in the manufacturing sector
Micro-factory solutions open new horizons for manufacturers, who typically must prioritise technology in terms of investment. The investment can be reduced thanks to a wide range of available European funding mechanisms. In that case, efficiency would be the unique word that defines Micro-factories. The first reason to jump into a micro-factory system is cost saving. The good thing about micro-factories is that only specific cells or components must be changed, making maintenance easier. Moreover, everything is standardised, even environmental parameters.
Another reason to find the micro-factory trend attractive is its capacity to produce highly personalised products and services. Even if the manufacturer has a hard time identifying the tailored need, agile and automated systems facilitate quick changes in production requirements. The main difference between conventional and micro factories is the lower power and resource consumption: localised production helps to shorten the transportation of goods, as much as the cost and carbon emissions.
The cutting-edge solution for science, the case of Fieldmade
Fieldmade, a tech-savvy company from Norway with its main office in Oslo, specialises in deployable additive manufacturing and digital supply chains. The company develops mobile additive manufacturing micro factories. They aim to produce spare parts on demand at the point of need. Thanks to the funds accorded through a European project called Change2Twin, the company can now digitise their mobile factories. The consequences are tremendous since they can have better control of the environment and process stability, increase their ability to perform predictive maintenance and provide remote assistance: “We are able to extract more data from our microfactory, and this gives us a deeper understanding of our systems during deployment and -operation. Furthermore, it has increased our confidence in our NOMAD systems by backing up our hypotheses with data.”
Local impact: is globalization running into its last chapter?
A few years ago, Made in Europe, Horizon Europe co-programmed public-private partnership was adopted as the voice and driver for sustainable manufacturing in Europe based on joined expertise and resources. The programme is running for 7 years with a total budget of €1.8 billion. The main objective is to boost European manufacturing ecosystems towards global technology leadership, circular industries and flexibility. The Partnership wants to contribute to Europe’s competitive, green, digital, resilient and human-centric manufacturing industry. In addition, the report that presents the partnership clearly exposed the local perspective: “The Partnership will contribute strongly to the interaction among key players that steer and/or implement national and regional manufacturing innovation initiatives”.
Being geographically closer to customers also means being closer to their tastes and preferences. Authenticity is the new need, and the best way to serve it is to have the manufacturing companies next to your door. It not only gives more value to the product but also limits the price fluctuations that can happen due to a war, a pandemic, political tensions, or other out-of-control reasons. Jobs are also a legitimate concern since automation provokes fear among workers. Nevertheless, the local component in micro factories could be an asset for regions before being considered as a reference for a manufacturing jobs nest. Micro-factories can really make a difference in the near future, giving more power to the manufacturing sector to adopt a circular economy, creating jobs, and boosting productivity at a local level and cost.
Marjorie Grassler