In our digital twin maturity assessment programme (also known as Assessment Voucher) we had the pleasure to welcome Laboratorio Geométrico SL (WINKLE) as one of our successful beneficiaries. The company is a 3D filaments manufacturer from Spain and they teamed up with DIHBU – Digital Innovation Hub Industry 4.0 for the assessment of their readiness for a digital twin. We met with Emilio Vicente Herrán from WINKLE´s Quality Management Department and asked him about their experience from Change2Twin’s assessment scheme.
Emilio, could you briefly introduce your company – where is it located, how many employees it has and what does it specialize in?
Emilio Vicente Herrán: “Laboratorio Geométrico SL (WINKLE) is a manufacturer of 3D printing filament (filamento impresora 3D), located in the city of Salamanca, Spain. We started our activity in 2017, and since then, we have developed a broad product portfolio. On the one hand, we offer prime quality filaments for demanding merchant and professional users, such as PLA, ASA, etc. On the other hand, we are making strong R&D efforts into new materials such as ULTEM or PEEK to adapt their properties (mechanical strength or flame resistance) specially developed for the aerospace or automotive industry.”
Which Digital Innovation Hub carried out the digital twin maturity assessment for you?
Emilio Vicente Herrán: “The Digital Innovation Hub carried out the digital twin maturity assessment for us is DIHBU is a Spanish Private Non-Profit entity, focused on Industry 4.0 Key Enable Technologies promotion.”
Tell us more about the assessment process.
Emilio Vicente Herrán: “The extrusion process looks simple: a mixture of polymer pellets and dye is put into the extruder that heats them and gives them the plastic shape, it comes out in the form of a wire and after being tensioned it is rolled on a coil.
Yes, it looks too simple, but, in practice, a series of factors and parameters are involved: tension, extrusion or cooling temperature, etc. which in the first instance determine the final quality of the filament. These parameters, especially the temperature, vary depending on the type of filament being manufactured: PLA, ABS, etc.
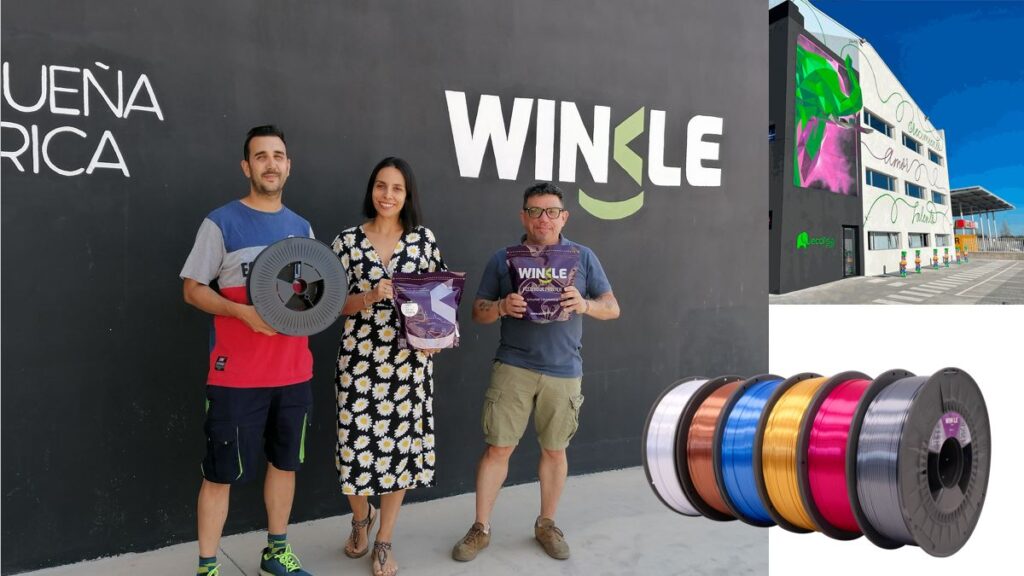
Making real experiments, for example, to have a filament with special mechanical properties is too expensive; to give just one example, the price of a Peek-SC kg is 720 €. That is why We thought of a solution that could allow us the “simulation of the recipes”, being able to play with those parameters of extrusion and cooling temperature, speed, etc., and establish different combinations to achieve the ideal filament, with significant savings in time, raw materials and personnel costs that this entails. A Digital Twin was the best solution to the simulation of these recipes. However, our final objective would be to have a holistic system that allows us to monitor all processes and analyze the quality of our filaments in real-time, detecting any anomaly that occurs in real-time.”
Now that the assessment is completed, are you planning to create your own digital twin?
Emilio Vicente Herrán: “Change2Twin has allowed us to work with experts such as DIHBU and ITCL on the definition and design phase of our Digital Twin; nowadays we are working on the development of an IoT system in the actual production lines, ready to be extended in case of the plant growth or the automation of any of its processes. After that, we will be able to start working on the development and implementation of the digital twin.”
Thank you very much for being part of Change2Twin assessment programme, we wish you and your team all the success!