Today we would like to introduce you Sangalli SPA, our beneficiary from Italy, specializing in road works and technological infrastructures. With Change2Twin funding they created a cognitive digital twin which consists of advanced modelling and machine learning techniques from data acquired by the equipment. We interviewed Raffaella Donghi, the company’s CFO, to tell us more about their digital twin.
First of all, can you please introduce your company?
Sangalli SPA is located in Mapello in the province of Bergamo and has over 100 employees. The company specializes in the construction and maintenance of roads, technological infrastructures such as aqueducts and sewers, as well as in the production of bituminous conglomerate and concrete.
What is the purpose of the digital twin that you have created?
The process to create a construction site in Sangalli SpA has been done completely manually. In fact, quoting and budgeting were carried out by an operator who performed the calculation manually without support from a mathematical model/algorithm. In addition, the execution phase (i.e., the milling phase) was handled manually so that the operator of that activity did not know the amount of asphalt he was milling or even what the daily target was that he had to achieve. Given the great effort required to digitize all the phases, it was decided to devote this experiment only to focus on the milling phase, the cost control and monitoring.
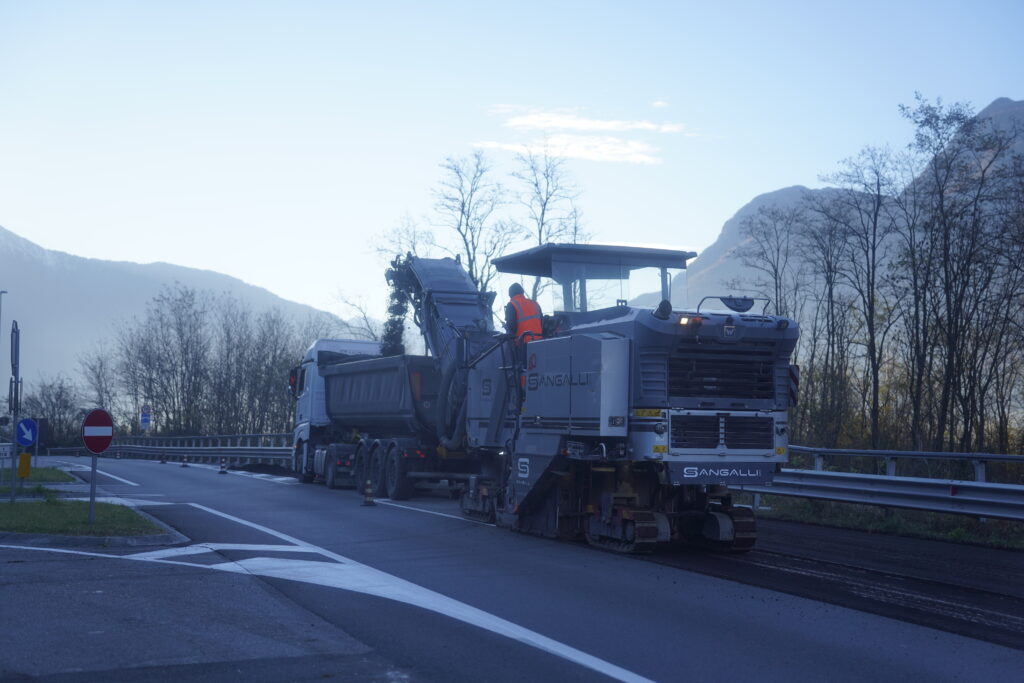
This enables Sangalli to know in real time how many tons of asphalt were milled. The digital twin experiment provided the possibility to connect the production and logistics process directly with the process of milling. The main target of the digital twin is to identify, realize and test a digital solution to collect a significant amount of data – usable in real time – in order to create “construction site organization models” more precisely. This model must guarantee a real-time control of construction site progress, with immediate management and control of production and costs, optimize resources and minimize the use of raw material and waste production and, in the future, as next step, allows decision support. Now, at the end of this project, we are testing a digital innovative system to support our planning and controlling production activity. Ultimately, we will be able to reach a decision support model, based on Machine Learning processes.
Has the digital twin fulfilled your expectations? Which improvements did it bring for your company?
The cognitive digital twin consists of advanced modelling and machine learning techniques from data acquired by the equipment. The system improves the analysis of Sangalli’s operational KPIs (resource optimization, cost savings, reduction of downtime) and enables smarter budgeting and planning of subsequent construction sites. Furthermore, it improves the real-time control of construction sites, optimization of asphalt production planning, monitoring of construction progress and logistics scheduling. The digital twin uses an AI-based platform for tracking flooring activities, suggesting the right combination of resources for the next construction site and data collection from machines involved in the production process.
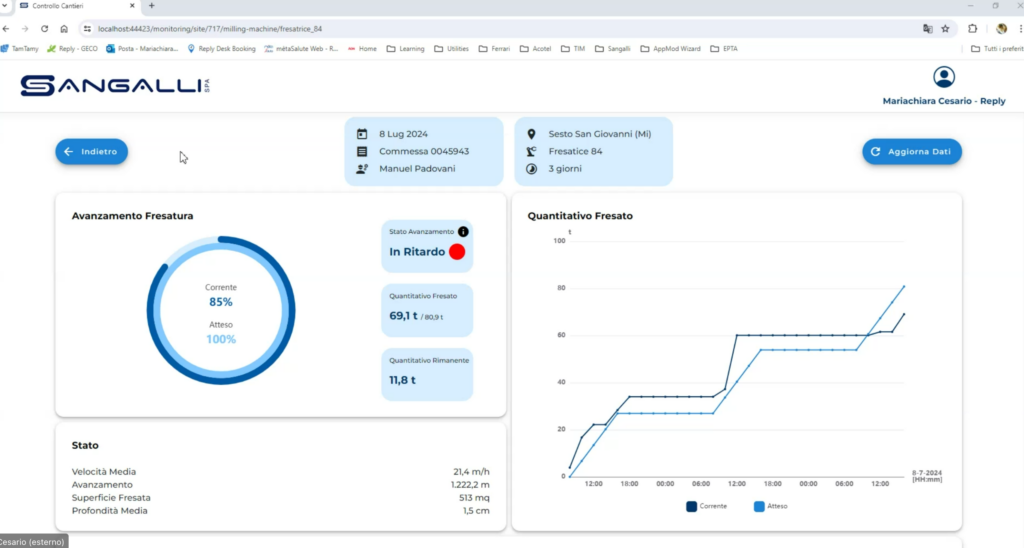
What are your plans for the near future with the digital twin?
This project has led to different positive impacts:
– possibility to transfer the applied approaches (sensorization of work machines, monitoring model and control platform) to the remaining processes of paving and paving of asphalt;
– possibility to connect the model results with which it is possible to monitor the construction site to the previous phases.
In fact, it will be possible to make this model as input of the algorithms needed to digitize the quotation and resource planning phase. The final target is the ideal development of a machine learning algorithm able to read input of the costs and activities monitored by this solution as elements for boosting its training in order to give cost forecasts and related planning more accurate.
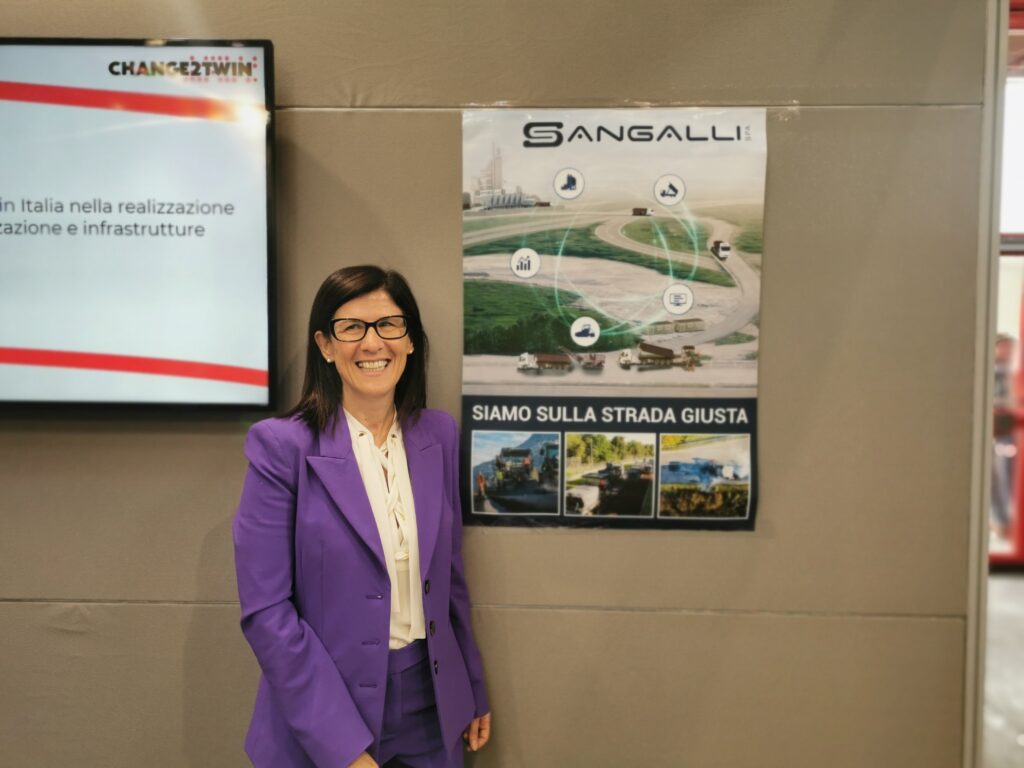
Raffaella Donghi
CFO
Sangalli SPA, Italy
“It was the first implementation of a digital twin. The project started from an idea that most people in our industry would consider unfeasible; the more the project advanced, the more we realized we were on the right track. These results convinced us that the digital twin solution is not only applicable to our processes but also delivers extraordinary results.”