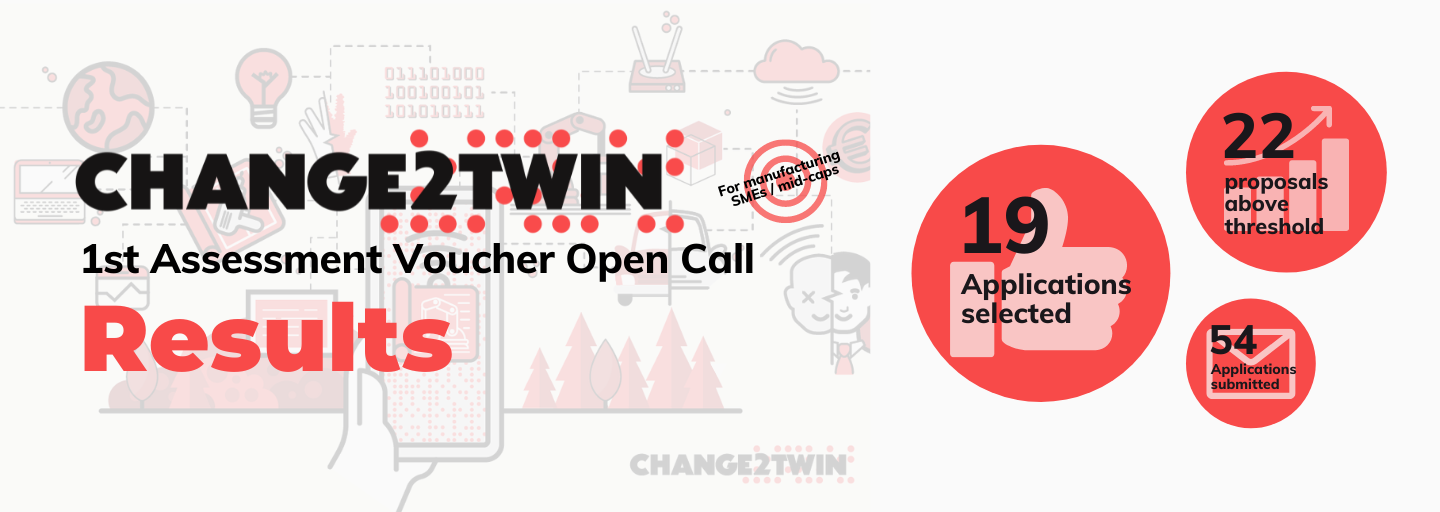
On the 29th of March 2021, the first Assessment Voucher Open Call of Change2Twin was closed, with 54 proposals submitted from 13 different European countries. Since the closure of the call, the proposals went through a rigorous, multi-step selection process, to identify the best applicants to obtain a qualified assessment of their digitisation capabilities by a Digital Innovation Hub.
Meet the selected companies
- Industrie Saleri Italo S.p.A. (Italy)
Saleri is a leading company in the design, development and production of water pumps and cooling systems for the automotive industry. The company mainly aims to improve the design of new components thanks to the digital twin, to make the design process more effective and robust, and to support engineers in decision making.
- MAROVT proizvodno izvozno uvozno podjetje, d.o.o. (Slovenia)
Marovt believes that digital twins can be used to simulate data for various purposes, exploiting a real time synchronization of the sensed data, thus being able to decide between a set of actions and execute the whole production system in an optimal way. This will result in higher efficiency, accuracy and economic benefits.
- CARPATIS SRL (Romania)
The Romanian meat product manufacturer aims to automate the slicing part and to include smart labelling in their process. They will explore the development of digital twins to track the flow of products through the supply chain, from the factory to the retail store, by collecting valuable insights from aggregated data produced by large numbers of electronic shelf labels.
- SC NORD ARIN PRODCOM SRL (Romania)
Nordarin’s vision for the next 5 years is to become a European leader in custom design-focused solid furniture for living & dining. They will assess how the use of digital twins would simulate and optimize the wood cutting operations, saving machine occupation time, unsuccessful attempts and avoiding collisions. And secondarily, they will inspect the potential of digital twins to enhance a virtual showroom.
- SAFESTEEL SRL (Romania)
One of their business lines is dedicated to manufacturing metal constructions & component parts of metal structures. In this area, SAFESTEEL aims at implementing digital twin technology for virtual design, optimization and best quality, and smart logistics. The objective is to create a model-based system engineering based on a zero-waste production process.
- ELVEZ d.o.o. (Slovenia)
This manufacturing company wants to assess and improve their digitalisation level in order to introduce real-time KPIs and visual boards in the sales department. They primarily aim at supporting operators in production and maintenance, planning services and storage, and to support team managers across finance, accounting, and controlling processes.
- METALMECANICAS HERJIMAR SL (Spain)
A Digital Twin would be a key tool for this SME’s digital lean manufacturing strategy. It would lead to a clear representation and understanding of welding tasks over heavy and complex infrastructure constructions. A Digital Twin will help them accurately analyze defects and product lifecycle inefficiencies, and therefore reduce labor risks indicators.
- Takumi Precision Engineering (Ireland)
The Irish company expects that the assessment will help them understand how to better track and trace orders, simulate production processes, increase collaborative design and improve predictive capacity. They aim at evaluating if a digital replica can enable them to make better and more informed decisions, so as to add value with the use of a model of linking data, models and processes.
- Total Precision Limited (Ireland)
The company uses an Enterprise Resource Planning system to improve management and timing involved in the production process. The data is currently being captured through excel spreadsheets. With the exploration of their digital readiness, they want digital twins to help the team understand the monitoring, usability, predictive capacity and adaptability process of data at a greater level.
- Salvagnini Maschinenbau GmbH (Austria)
Salvagnini manufactures and distributes high-quality automatic panel bending machines and manufacturing centres for the fabrication of metal products. Digital twin technology is already used to calculate optimal tool path trajectories and compensate for material variations. However, the digital twin must be manually adjusted during commissioning, so they now envision an adaptable digital twin that automatically adapts to each machine during commissioning, and is autonomously updated during operational life.
- E.CIMA, S.A.U. (Spain)
The Spanish SME looks for better traceability in order to observe and anticipate technical problems, as well as to identify the points of improvement of the production process. Therefore, the implementation of a digital twin will allow them to have information about each of the production processes.
- Neutroplast – Indústria de Embalagens Plásticas (Portugal)
To better respond to customer needs and improve process control, the packaging SME aims to implement a digital twin of its production system to help take decisions in process optimization and planning, to evaluate product quality with data, and increase predictive capabilities in maintenance. The system is intended to increase operators’ performance, replacing corrective with predictive maintenance.
- MARINA RACE S.L (Spain)
The implementation of a digital twin within Marina Race will allow providing feedback on the manufacturing status to their customers automatically, improving their reliability and traceability at all order and manufacturing stages. This will facilitate the creation of a virtual ID for each of their suits, simplifying the FIA certification at all times.
- Jasil – J. ANTONIO DA SILVA, LDA (Portugal)
JASIL intends to implement a solution that allows the acquisition of streaming data from the production process and critical dimensions of all the parts produced. Its treatment would be in almost real time, autonomously off the operators, that could provide on-time information about nonconformities, considering the descriptive perspectives (what nonconformities occurred), diagnosis (why they occurred) and predictive (when they will probably occur).
- MobyFly SA (Switzerland)
The digital twin modeling and data assimilation capabilities will support MobyFly’s boats development process, leveraging the team’s know-how. The goal is to perform better in terms of both supply and delivery reliability within its three production processes: preparation for physical production, tracking of these key components production, and management of the boat’s assembly.
- SIA “JELGAVAS TIPOGRAFIJA” (Latvia)
A printed book consists of approximately 10 components and its production process includes pre-processing, printing, and post-processing stages.The digital twin would transform the process,increasing its agility, the efficiency of material and equipment usage; improving the traceability of manufacturing process-related decisions; decreasing dependence on the personnel’s tacit knowledge; and shortening the response time to book manufacturing enquiries and better customer service.
- DNAPhone Srl (Italy)
DNAPhone Srl company develops diagnostic systems for quality controls for food and beverage through optical devices. By comparing real-life and digital twin behaviours they will be able to study the durability of electronic components such as LEDs, diagnose and detect production and commissioning faults or anomalies, and monitor the overall performance evolution over time.
- Simem SPA (Italy)
The performances of their concrete plants are determined by the setup of all the parameters of the automation during the on-field commissioning. There are multiple variables and boundary conditions that affect the calibration, and operators test production manually. Real time feedback by a Digital Twin and predictive analysis will speed up the process, dramatically reducing real testing and consequent errors.
- Evers Agro BV (Netherlands)
The soil treating products manufacturer has the purpose to have a digital twin that combines production and design. The aim is to programme the main welding robot involved in production in order its downtime to be reduced and its data to be gathered and analysed for planning and evaluation purposes. Also the uptime of the robot might be upgraded by offline programming through the potential digital twin.
Download here the full public report about the 1st Assessment Voucher Open Call:
What’s next?
The selected SMEs and mid-caps have signed a sub-grant agreement to receive a lump sum of up to 10 000 Euro each, to be used with a certified DIH of their choice. They will get a detailed assessment of their current situation and three different “recipes” to implement a digital twin solution with the best components and providers in the European market. A total amount of 180 482,48 EUR is going to be distributed among the 19 winning proposals.
The applicants that have been selected will also be able to apply to the next open call of Change2Twin: the 1st Deployment Voucher open call. It will be open until the 30th September and it will provide the selected applicants with the following benefits:
- Up to 90 000 Euro as a lump sum to cover the costs to deploy and implement technology and systems applicable to digital twins for manufacturing.
- Technical mentorship to support the digital twin deployment in each phase of its implementation, from user requirements to design specification.
Apply to the Deployment Voucher!
Keep yourself informed by following the Change2Twin LinkedIn page and join the Change2Twin communityto find out more about digital twins, to network with colleagues and to be informed of all the opportunities to digitise your manufacturing SME or mid-cap.
The original article was published by Marta Albújar on Change2Twin Community.