Labormak is our digital twin champion from Northern Italy. They are a young company specializing in robotic cells. In Change2Twin they applied for creation of digital twin in intralogistics area. Their project is called Twin4Logs and the digital twin is now up and running. Therefore we asked Federico Fumagalli, Labormak’s Research and Development Engineer, to tell us more about their solution and the company’s future plans with the digital twin.
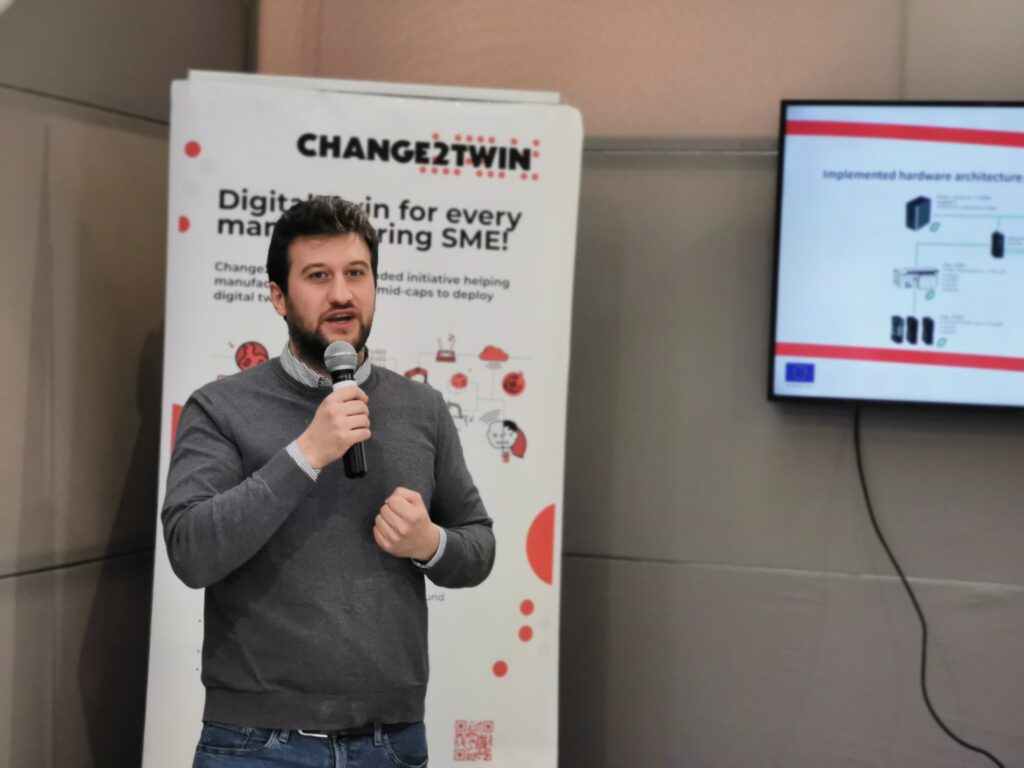
Federico, first of all, please introduce your company.
Federico Fumagalli: Labormak is an SME located in Piacenza, in northern Italy, counting approximately 30 employees. We are a young and dynamic company that, thanks to our team of engineers and designers, is constantly focused on continuous technological innovation. Our business is mainly divided into two categories: (1) Catalog solutions: We produce robotized cells for the automation of machine tools and for end-of-line palletization in the logistics industry; and (2) Custom solutions: We design and manufacture industrial prototypes of single elements or complex machinery for various fields of application, taking full or partial responsibility for the entire production process; from project conception to plant or machine installation and final testing.
What is the purpose of the digital twin that you have created?
Federico Fumagalli: Our digital twin supports us in the field of intralogistics, this is why we called Twin4Logs. The purpose of the digital twin is to perfectly integrate into the company’s workflow, effectively reducing the time and costs associated with various stages of operations. By providing a virtual replica of complex intralogistics plants, it enhances customer engagement by allowing them to visualize and understand proposed solutions more comprehensively. This integration ensures smoother transitions from the pre-sales phase to design activities and commissioning, streamlining the entire process.
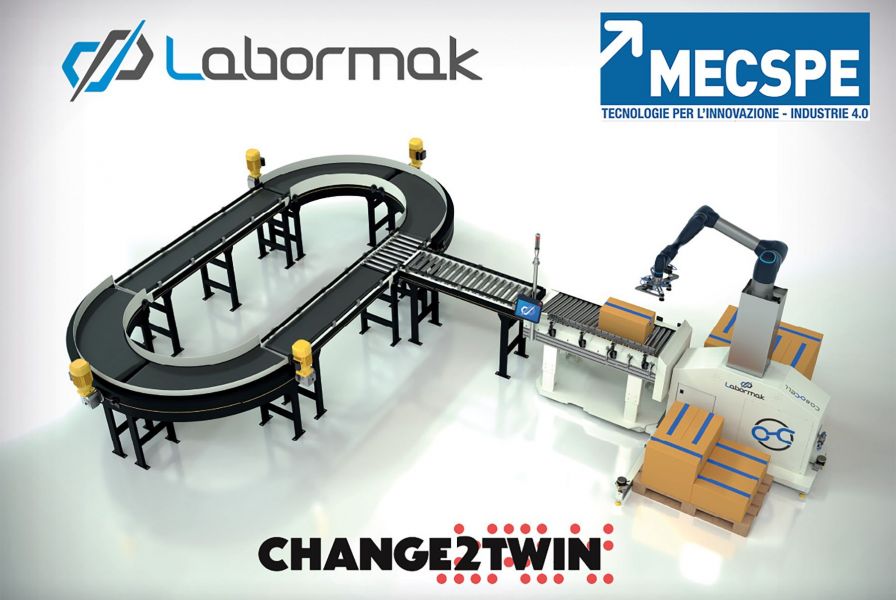
Moreover, the digital twin enables early-stage testing and validation, accelerating the identification and correction of performance issues offline, thus minimizing the time required for commissioning. Ultimately, by optimizing workflow efficiency, the digital twin initiative aims to enhance customer satisfaction, reduce costs, and drive overall operational excellence.
Has the digital twin fulfilled your expectations? Which improvements did it bring for your company?
Federico Fumagalli: While the results and expectations of the experiment will become clearer at the project’s end, our initial observations suggest promising outcomes aligned with our objectives. Particularly challenging to quantify are the benefits in the pre-sales phase, yet we have noticed a significant enhancement in layout preparation for offers and in the design phase.
The availability of an offline modeling tool has empowered us to swiftly recreate diverse layouts and conduct fairly accurate simulations. Moreover, this advanced tool facilitates the exploration of innovative ideas and the execution of initial offline developments, such as integrating IIoT devices and devising sustainability-oriented solutions.
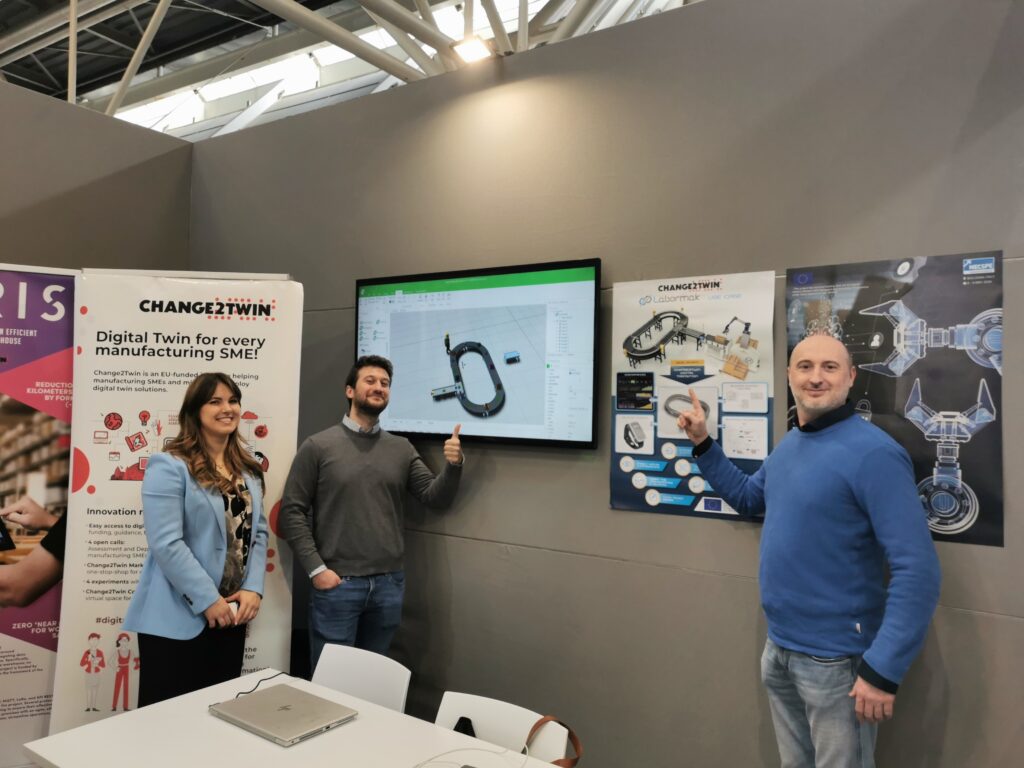
In the logistics realm, the digital twin enables the ideation and testing of control algorithms aimed at optimizing energy consumption. For lengthy and intricate production lines with various energy sources, equipping the lines with appropriate energy meters allows for measurement and comparison of different control software, leading to the attainment of the best results for the specific application.
Overall, while the precise impact of the digital twin will become clearer with further assessment, its contributions to layout preparation, design efficiency, and innovation acceleration are evident and align with our aspirations.
What are Labormak’s plans for the near future with the digital twin?
Federico Fumagalli: Our future plans include turning the digital twin into a comprehensive corporate tool accessible to various roles within the company, regardless of their educational, cultural, or generational backgrounds.
Additionally, as part of the Change2Twin project, we have developed a virtual library of mechatronic objects tailored to the intralogistics domain, including conveyors, sorters, sensors, and more. To ensure smooth initial implementations, we’ve chosen basic elements to populate this library, with their modeling focused on fundamental behavioral aspects. However, our aim is to enhance this tool progressively by adding new elements and refining their mechatronic modeling based on continuously expanding data collection, thereby increasingly aligning with real-world behaviors.
This approach enables us to tackle more complex and inevitably profitable projects in the future.
Moreover, the development of a robust digital tool opens up innovative possibilities, including the integration of IIoT technologies for human-machine interaction and data collection and analysis for purposes such as energy consumption optimization algorithms.
By developing and testing these technologies on a virtual model, we can significantly accelerate research and development activities in this area, driving forward innovation within Labormak.
Federico Fumagalli
R&D Engineer
Labormak, Italy
Labormak’s first experience with the digital twin has yielded compelling results. What initially seemed like a futuristic concept unfolded into a practical solution as we progressed.