As a global producer of paints, finishes, mortars, putties, primers and treatments, Graphenstone has factories in Spain, China, Malaysia, Australia and Panama.
Currently, the company relies on analogous documentation. The entire Graphenstone process was based on a sheet of paper that was moved from stage manually and generated errors due to loss or misplacement of the production order, losing control of the process .Therefore, the major digital innovation goal is the optimization and automation of documentation. In particular, the material and warehouse management should be optimized in tight relation with the production process in order to enable:
- a real-time-inventory,
- the product traceability and documentation,
- an additional service for the customer in digital representation of the product, and
- a dramatic reduction of time for inventories.

A series of use case workshops helped to identify three major digitization challenges for Graphenstone. Those are the digitization of the production process, the digitization of the raw material warehouse and the digitization of the product information.
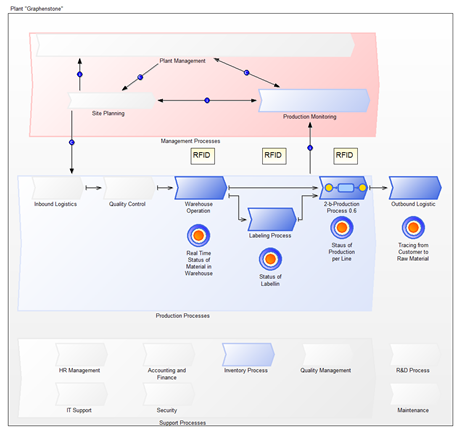
The plant process map (depicted above) highlights the processes that are in the focus of this use case:
- Warehouse Operations – The main interest with respect to the warehouse operation is how to enable a real time inventory.
- Labelling Process – The labelling should facilitate not only product descriptions but digitally lift the buckets with RFID tags providing for instance production process details.
- Production Process – Based on the production process, production line monitoring is introduced for showing the current order on the line.
- Product Tracing – Product tracing is enabled by attaching information such as the production order, laboratory approval certificates or raw material information directly to the product buckets in order to provide added value to the customer.
The overall complexity of the production processes could be simplified by applying means of abstraction on the business processes identified during the assessment – consisting of the usage of the Change2Twin Compass Tool, the application of process modelling by applying the BPMN 2.0 standard, expert guided modelling workshops, the development of a physical experiment and the conduction of cocreation workshops – and resulted in following high-level production process:
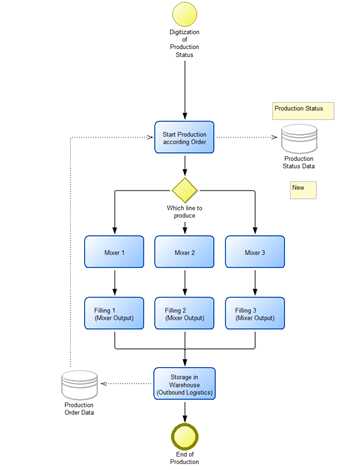
To generate the traceability data that can feed the digital twin model. A software system has been developed by CT INGENIEROS for the control and management of manufacturing and labelling orders in Graphenstone. This software system is a multi-device platform in which to carry out all the operations that affect a manufacturing order for the management and control that were previously manual in a digital way).
For this, all cans and manufacturing orders will be tagged with RFID tags and the states will be updated depending on the state in which they are (oven, laboratory, quality, packaging, warehouse, etc). This has allowed the possibility of locating or controlling manufacturing orders in real time.
In addition, these sensorization of the manufacturing orders has allowed the creation of stations (sensor + microcontroller) in the places where the raw material is stored, so that a stock control of the raw material can be generated (an IoT system in the factory).
The data provided by the Graphenstone erp has made it possible to create a local data structure without modifying the erp due to customer requirements and not affecting production, allowing traceability and sending the information to the digital twin model emulated by BOC. The information is sent from the generated system to the digital twin through a rest api.
RFID labels are added in the current equating process, adding an added value to the generated product, so that no product is lost and generates information allowing us to anticipate bottlenecks, through the info of the digital twin of the production order.
The Graphenstone use case has to deal with additional challenges due to completely analogous machines, which are out of scope to twin within Change2Twin. For this reason, the twinning objective is to develop a digital twin of the business/production process – respectively the organization –, to generate behavioural simulations.
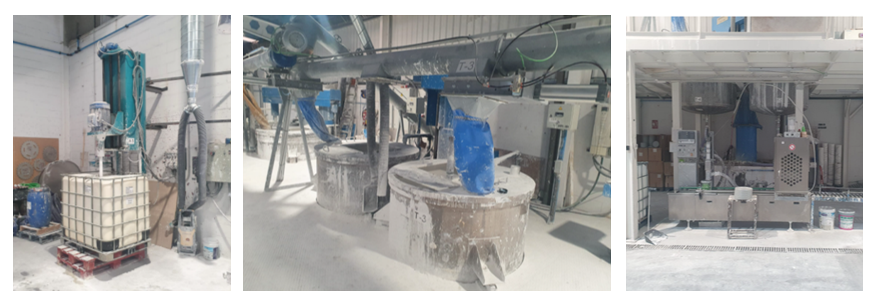
According to Gartner, a digital twin of an organization enables an organization to adapt. This transformation journey ranges from the identification of business processes over the creation of awareness supported by the physical experiment to informed decision making. To achieve this goal, digital information of the production process, the material flow and the labelling is generated. The focus was set on raw material flow, the production process and the labelling process. The selected processes are most promising to achieve the goal of creating a digital twin of the production process. Furthermore, they have the potential to add additional value to Graphenstone’s current manual approach. In particular, the information gained by digitizing documentation and warehouse monitoring enables value creation by means of simulation based on the collected data.
Thus far, a physical paint production experiment conducted in the OMiLAB Innovation Corner provided by BOC served as a foundation to identify the relevant digitization infrastructure. So far insights on how to support a digital twin with the conduction of a physical experiment could be gained. The pilot is seen as innovation action including open-source prototypes on ADOxx.org. RFID readers are currently installed on the Graphenstone production site to monitor the production processes and facilitate the digital innovation goals.